MAKING RAILWAY ASSETS INTELLIGENT WITH IOT AND DATA ANALYTICS
Sambi Reddy Bhimavarapu, B. Tech in Electronics and Communication Engineering, Chief Engineer, Efftronics Systems Pvt. Ltd.
Anvesh Dasari, BS in Electrical Engineering, Vice President, Efftronics Systems Pvt. Ltd.
Bhavani Shankar Surabhi, M. Sc in Electronics, Executive Manager – R&D, Efftronics Systems Pvt. Ltd.
Summary
Asset management is a quintessential part of Railway infrastructure maintenance as it is the basis of efficient train operations. As a part of Indian Railways march towards 4th Industrial Revolution, to usher in greater efficiencies, it is imperative to understand the interconnectedness of assets, data, and processes. This paper presents value centric six-stage approach for making railway assets intelligent with IoT and Data Analytics and strive towards establishing intelligent digital infrastructure in line with Industry 4.0 digitalization expectations. It also proposes cross-industry collaborative working model between Indian Railways, OEMs, and IoT vendors. The success of making assets intelligent and achieve the intended value depends on how well integration of existing processes into the intelligent digital infrastructure happens.
Introduction
Industry 4.0 goes beyond the connection of IT applications and physical assets. Industry 4.0 has inspired countries across the globe to take up nationally driven industrial digitalization and productivity programs, policies, and initiatives designed to digitalize various sectors and promote new business models that boost economic competitiveness. Internet of Things (IoT) forms the digital foundation for intelligent infrastructure. By embedding sensors or capturing asset diagnostics through its communication interface, IoT systems enable assets to be digitalized, thus making them potential for various use cases. Even though IoT systems generate asset data, the key is to translate data into actions or in other words drive new value which is possible through algorithms/data analytics.
Figure 1: March towards Industry 4.0 – from systems in silos to system of systems
In practice, intelligent asset management is all about collecting, consolidating, and processing, accurate, timely and high-quality data about various assets, as a means of deriving insights about their current and future state. It’s also about routing these insights to appropriate stakeholders, including field staff, immediate supervisors, and officers in-charge to enable data driven decisions through analytics and ensure appropriate value actions are taken.
Challenges for Indian Railways Signaling & Telecommunication
- Distributed, sophisticated and complex equipment installed in the field affected by dust, humidity, heat & electrical surges
- Insufficiently skilled maintenance personnel
- Rapid introduction of new technologies
- Dependency on other departments
- Containing the cost of maintenance
Internet of Things (IoT)
The internet of Things (IoT) is the network of physical or virtual things that has the ability to sense/capture information in real time through sensors, intelligent things & Apps, communicate through wired / wireless in variety of protocols, analyse information on the fly and derive insights, and act through data-driven decisions and achieve value outcomes.
Figure 2: Internet of Things – Characteristics
An end-to-end IoT solution is a heterogeneous mix of IT and operational technology (OT) assets, IoT Gateways, and a robust software platform. A typical IoT solution contains three tiers. As discussed, tiers define where a component, function or process operates in the architecture. In other words, tiers are logical deployment locations.
- The Edge tier is where data is sampled and collected from the physical world by “things” or devices. These “things” may include consumer devices, appliances or industrial that contain sensors to collect data, or actuators to alter the operation of the device/system. The edge tier may also contain optional IoT gateway that provide localized data analysis, event processing and storage, as well as help integrate legacy devices to IoT platforms.
- The platform tier is where the IoT system aggregates systemwide data and events from many edge locations. It will perform both event processing and stream processing. As you can see, it also does device management, orchestrates tasks or invoke enterprise applications.
- The enterprise tier is where IoT integrates with the wide range of business applications, processes and services required to accomplish a business objective and enables data driven decision making. Typically, APIs are used for this purpose
Spectrum of Analytics
Even though IoT systems generate asset data, the key is to translate data into actions which is possible through data analytics / algorithms.
Contextual analytics will help in –
- Optimisation of maintenance effort
- Deskilling of maintenance personnel
- Improving availability of the system
Figure 4 – Spectrum of Analytics
The maintenance process through IoT system
- Sensing parameters & generation of data
- Communicating sensed data to central location
- Applying algorithms to generate actionable decisions by IOT system
- Assessment of maintenance staff
- Taking decision based on human input and output from IoT
- Implementation of decision
Stages 1, 2 & 3 are contributed by IoT system
Modern assets have intelligent diagnostics in-built, whereas legacy systems need augmentation of IoT sensors for real time capture of their behaviour and health. Thus, various IoT devices like intelligent sensors, Edge devices, Processing Units and Gateways will be deployed for monitoring of existing railway infrastructure making them intelligent and ready for advanced analytics. Based on operational behaviour of railways assets, data generated will be both continuous time series and also irregular and sporadic in nature. Data ingestion, stream processing/event processing and contextual analytical algorithms has to be designed for that behaviour.
Value from IoT systems
Value is defined as “The performance of actions that increase the worth of goods, services or even a business”. The value creation should be seen in the context of creating better value for customers purchasing products/services. Mathematically it can be derived as
Value = Overall benefits / Lifetime ownership cost
It is important to understand the value loop which has five stages.
- Identify the value
- Create the value
- Deliver the value
- Scale the value
- Refine the value
Thus, the value from IoT Systems in view of signaling system is to
- Ensure availability of signaling system
- Reduce MTTR – insights of failures
- Increase MTBF – insights into system
through predictive alarms, real time simulation and health reports
- Deskilling of maintenance activities
- Collaborative of maintenance activities
- Reduction of maintenance effort
- Provide data driven decisions
Figure 5 – Moving from periodical to predictive maintenance
The value outcomes can only be achieved when IoT systems evolve into full-fledged predictive maintenance systems driven by data thus improving the performance of the system.
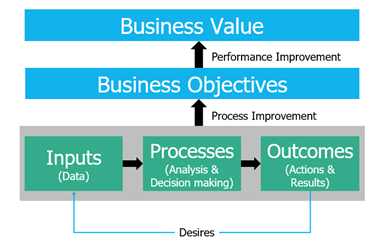
Figure 6 – Business Value is driven by Analysis and Decision Making
Solution Approach
To build intelligent infrastructure inline with Industry 4.0 expectation, Indian Railways has to put in place – a high performance, and reliable IoT infrastructure. This should be ably supported by a high through-put with minimal latency communication and routing infrastructure, and a robust IoT platform. IoT infrastructure should be capable of real-time processing and analysis of data, contextualizing raw data into meaningful information and asset-related insights… with data analytics, data visualization, and data dissemination capabilities. And this is not one-time adhoc execution but rather a systemic six stage process.
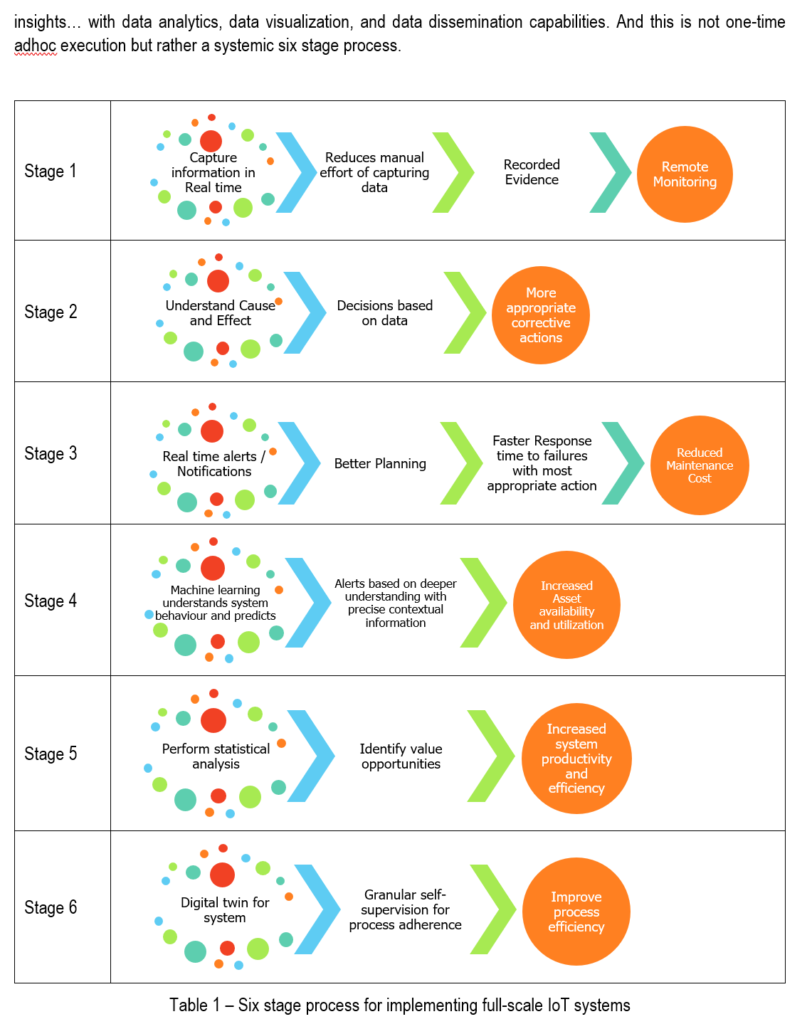
Stage 1
Initially, all signaling assets of railways needs deployment of IoT devices augmented with sensors and interface ports to capture asset related data in real-time. This enables remote condition monitoring of assets and also creates recorded evidence. IoT devices could be of two types – condition monitoring with external sensors, condition monitoring through diagnostic information through interface ports.
This information when presented in the form of descriptive analytics will be useful for railway personnel to discharge their duties much more efficiently.
Official | Role | |
1 | Maintainer | Action – Hands on rectification of failure |
2 | Supervisor | Delegation – Takes responsibility to delegate to another maintainer in case the regular maintainer fails & instructs maintainer on how to rectify the failure. Sometimes, he himself may attend and rectify the failure |
3 | Junior Engineer | Monitors – Guides – ensures failures are rectified without delay |
4 | Senior engineer | Information – Personally, looks at failures with big impact on train running or safety related alarms |
Table 1 – Four Levels of reporting personnel and their responsibilities
Stage 2
In this stage, all assets behavioural characteristics are captured in various cause-effect scenarios. Domain knowledge is used to establish probable causes for each possible effect for each type of asset. Diagnostic analytics is used to describe cause-effect relationship for an asset behaviour. If actual causes are known to maintenance personnel, more appropriate corrective actions can be taken based on true picture thus reducing the mean time to repair (MTTR).
Cause | Effect as seen by humans | Effect as seen by IOT system | Example of Effects as seen by IOT system | |
1 | Cause 1 | Effect (A) Point failed [same for all 3 causes] | Effect 1 | Point machine not operated |
2 | Cause 2 | Effect 2 | Point machine not locked | |
3 | Cause 3 | Effect 3 | Point machine locked | |
4 | Cause 4 | Effect (B) Point flashing [same for both causes] | Effect 4 | Point loose packing |
5 | Cause 5 | Effect 5 | Point mis-adjustment |
Table 2 – Cause-Effect relationship identification for a signal asset’s behaviour
IoT System empowered by diagnostic analytics will help in greatly reducing the maintenance effort by eliminating some of the manual maintenance activities and by reducing frequency of maintenance.
Activity | Period |
Cleanliness, lubrication – point & point machine Tightness of fittings [bolts & nuts]Wear and tear of point machine parts Safety and reliability test of detection | Fortnight |
Electrical parameters – voltage, current,Friction clutchOverload protection with time delay | Month |
Joint track check with track supervisor | Quarter |
Greasing & oiling of point machine | Quarter |
Point motor insulation Tail cables insulation | Half-year |
Table 3 – Maintenance Schedule for signaling asset – Point
Schedule Code: EP1 | Cause (Deficiency) | Effect detection (Failure) | How detected | |
Check the following | ||||
1 | The machine for tightness | Machine fixing bolts loose | Current signature – not smooth Higher vibration while train passing | Sensing electrical current consumption pattern and vibration |
and free from rust & dirt | ||||
2 | Cleaning, graphite/oiling of slide chairs and assembly up to 3 sleepers from the toe of switch by signal staff | More friction | More effort for point operation | Current signature (more energy) |
Table 4 – Reimagined cause-effect analysis for point maintenance through condition monitoring (Sample)
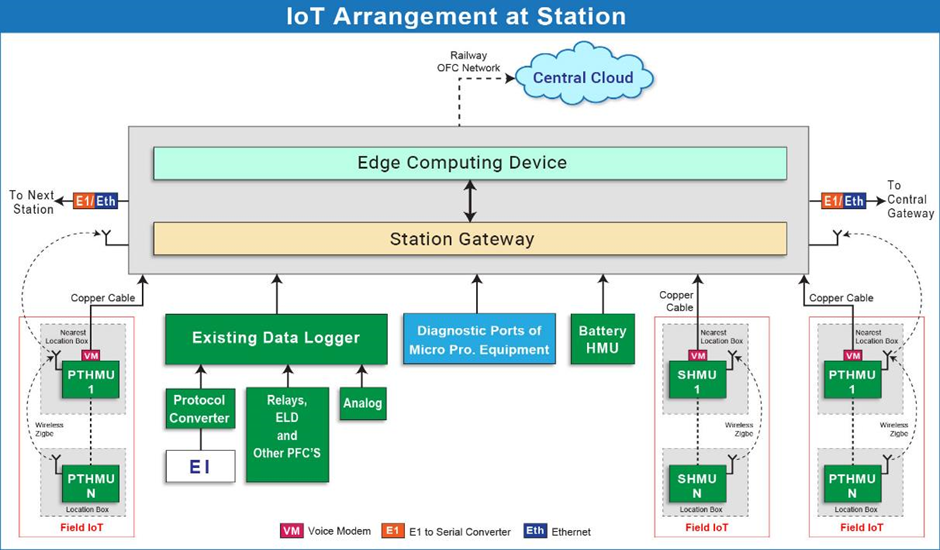
Stage 3
In this stage, based on diagnostic analytics and conditional fault-logics, real-time alerts / notifications are disseminated for better planning which leads to faster response time to failures with most appropriate action thus reducing overall maintenance cost.
Level | Criteria | |
1 | P1 | Causes stoppage of traffic Causes safety infringement |
2 | P2 | Causes stoppage of traffic if not rectified in few hours |
3 | P3 | Indicates deviation in equipment parameters which is likely to cause failure in future |
4 | P4 | Miscellaneous incidences (Ex: Statistical purpose) |
Table 5 – Four levels of notification based on priority
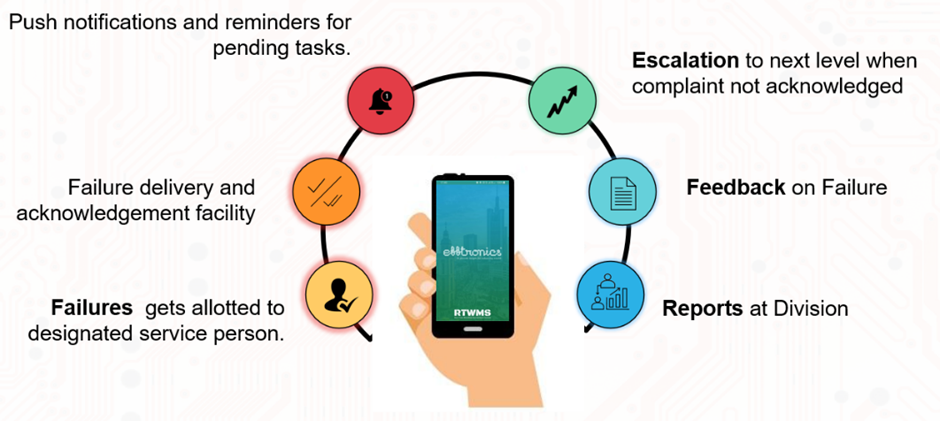
Figure 8 – Notification lifecycle
Stage 4
In this stage, machine learning is introduced and taught with all cause-effect scenarios thus allowing IoT system to provide predictive alerts with precise contextual information. This will tremendously improve asset availability and utilization. Classification algorithm is the more suitable supervised machine learning algorithm for predicting the failure of a railway signaling assets based on data patterns of electrical, digital and physical parameters.
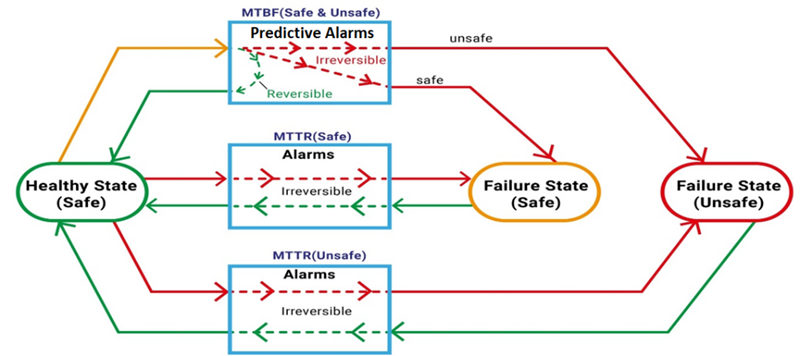
Figure 9 – Failure state analysis model for signaling element
Stage 5
In this stage, extensive statistical analysis is performed on asset operational data and failure data in the context of optimizing the operations and achieve increased productivity and efficiency across entire chain of train operations. Analytics may start with recognition of combination & sequence of events. Subjecting this data to machine learning algorithms to
- Recognize patterns for known failures
- Looking at unknown patterns in data and interpret state of the system
- Leading to artificial intelligence
Once analytical ecosystem is in place, then railways is in a position to implement collaborative working withing railways team with proper escalation hierarchy.
- Technician – responsible for restoration of failure by hands-on action
- Supervisor – assists the technician
- Officer – guides the supervisor – he monitors the system
- Overall in-charge officer – responsible for the overall system
Stage 6
In this stage IoT system will evolve into system of systems which can be visualized as digital twin for entire signaling system of Indian Railways. Digital twin helps railways to have granular supervision for process adherence and helps in improving overall process efficiency and performance of signaling system. It provides single source of truth for all stakeholders. Digital twin
- Identifies traffic bottle necks on real time basis
- Suggests best option for train movement to train traffic controller
- Optimum usage of fixed & movable [track & train] assets & human resources
- Identifies traffic bottlenecks due to infrastructure limitation
- Suggests solutions for improving line capacity to infrastructure planners
- Improves operational efficiency by
- identifying mistakes of signal operators & loco pilots
- Helps safe operations – detecting unsafe operations – behavior of human & equipment
- Helps in improving accountability of railway personnel and Ensures actions are performed
Way forward
As majority of technology providers doesn’t have proper understanding of railway signaling system, it is in the best interest of railways to share required domain knowledge with IoT solution providers for successful implementation of new age technologies in railways.
With technological change, it is imperative to re-engineer the existing processes. As test room is the core of asset maintenance, it needs re-organization to support collaborative working.
Test room to be manned by two levels of staff.
Responsibilities of Level 1 staff
- Ensuring timely action on alarms generated – i.e., correctness of alarm, alarm delivery to maintainer, coordinating with traffic controller
- Coordinating with OEM of IoT HMUs – in case of wrong alarm generation or no alarm generation or data logger / IOT device failure
Responsibilities of Level 2 staff
- Assists the maintainer in rectification of fault
- Coordinates with OEM of signalling equipment – in failure rectification
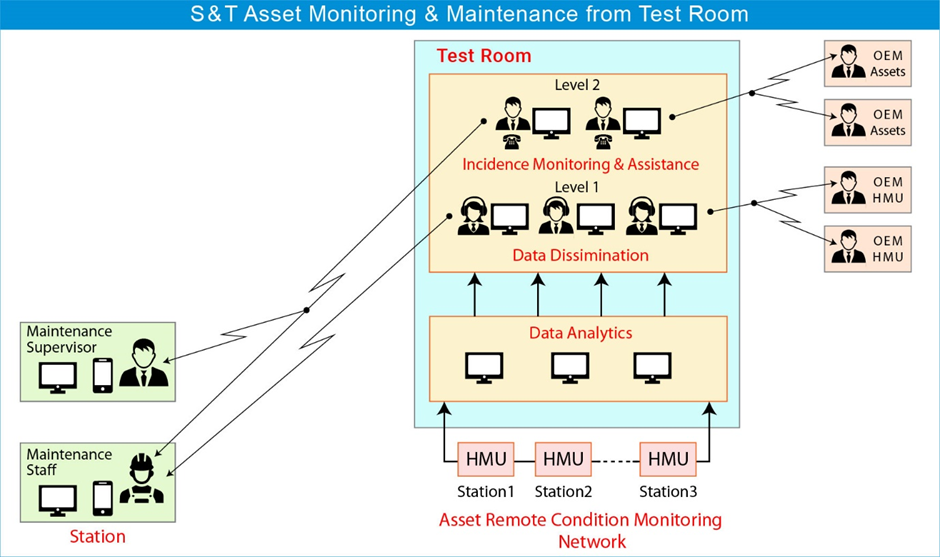
Figure 10 – Proposed collaborative working from test room / command centre
At the same time, Industry also expected to invest in analytical knowledge of signaling system, prepare for long term relationship than one-time solution and collaborative working with railways & OEMs of signaling systems.
Digitalization of logistics processes is not core IoT activity or Industry 4.0 expectation. Digitalizing bad process gives poor outcomes. Hence, in order to have successful digital transformation, process re-engineering is must. We recommend Indian railways to look at our proposed 6-stage approach in their march towards Industry 4.0 with value outcomes.
References
- “Jump-Start your Industrie 4.0 initiative by leveraging business moments”, Alexander Hoeppe and Don Scheibenreif, Gartner Inc.
- “Succeed with your Industrie 4.0 initiative through efficient program governance”, Frank Ridder, Bettina Tratz-Ryan, and Axel Jacobs, Gartner Inc.
- “Build your blueprint for the Internet of Things, based on five architectural components”, Saniye Burcu Alaybeyi, Jim Tully, and Nick Jones, Gartner Inc.
- “Designing an IoT reference architecture”, Paul Debeasi, Gartner Inc.
- “A guidance framework for architecting the Internet of Things Edge”, Paul DeBeasi, Gartner Inc.
- “The Internet of Things Reference Model”, White Paper, CISCO
- Indian Railways Signal Engineering Manual